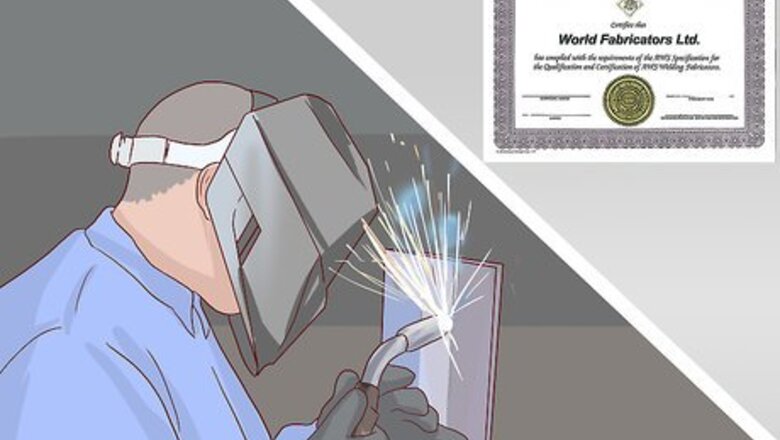
views
Preparing for the Test
Decide which welding certification applies to the work you want to do. In the USA, there are many federal and state laws and regulations, and governing bodies that enforce and require certain building codes, rules, and welding fabrication standards.
Learn the 6 major welding categories you will be tested on. Although, there are a vast number of different metal fabrication processes and techniques, the AWS certification tests mainly cover: Shielded Metal Arc Welding - SMAW. Gas Metal Arc Welding - GMAW. Flux Cored Arc Welding - FCAW. Gas Tungsten Arc Welding - GTAW. Oxy-fuel Gas Cutting and; Plasma Arc Cutting.
Study and follow all the A.W.S. (American Welding Society) standards (codes, specifications, recommended practices, methods, guides, etc.). Most types of metal fabrication will fall under one of the various AWS codes in USA. ASME - This code covers the same variety of metal fabrication types as AWS does, but in the USA it is used mainly for the production of pressure vessels and high pressure piping. API - This code covers the production of low pressure tanks and piping for the transport and storage of fuels and crude oil.
Find an updated copy of the test plate's blueprint. Practice every type of welding (methods, metals, thickness) and all body positioning, working space clearance, and weather conditions you could be tested on. The usual steel plate groove test for the AWS D1.1 code consists of two plates with a 45 degree inclusive angle (22.5 degree bevel on each plate). The bevels are placed facing each other, leaving 1/4" gap between the feather edges. A backing plate is tacked onto the back of the two plates to hold them together while the weld is completed.
Master welding the two most difficult positions and the thickest steel plate on the test. In the D1.1 test, you will commonly complete two positions: vertical up and overhead positions. If you pass both of these tests you will be qualified in all positions and if you complete the test using 1" thick plate you will be qualified from 1/8" to unlimited thickness.
Practice diligently until every weld is flawless and continuously uniform. The most common failures are found on initial visual examination. While the code does allow for discontinuities such as undercut, porosity and other issues, these are clues that an examiner will use to understand the skill level of the welder, so practice until your welds are as close to perfect as you can make them. This way when you you actually perform the test you will have already been harder on yourself then anyone else will be.
Invite over your most critical and perfectionist friends to nitpick your work. Don't rely on your supportive friends; they will only give you excuses instead of helping you get better.
Don't settle for a good-looking surface weld. A bad weld can be masked to look strong. If your weld passes visual inspection, then the next step is to perform destructive testing, otherwise known as the bend test. If the plate you welded was thicker than 3/8" then the test strips will be 3/8" strips cut from across the weld and will be bent to the side with the point of maximum stretch where the weld is. If the plate is less than 3/8" thick then two strips will be cut from each plate and these will be bent with one plate face out and the other root out to stretch each side. There should be no cracks, tears, flux inclusions or other defects. It should bend just like a solid bar would bend.
Avoiding Common Mistakes
Don't go too fast. Match the filler metal feed rate, depth and thickness of the weld, and the applied heat intensity to the speed rate of your welds.
Avoid incorrect settings on the welder. Double check every instrument you use and adjust all settings for the correct application.
Avoid improper storage, handling, and use of welding materials and supplies. If you use 7018 you need to keep the electrode in a rod oven to keep moisture out of the flux.
Take your time to clean any contaminant residue after every pass. This occurs most often when leaving flux behind. No, the next pass will not burn it out.
Ensure you achieve fusion on the sides of the weld. Completely infuse the entire joint area. It should be a smooth transition between filler weld metal and base metal.
Carefully read the entire instructions and double check every measurement of the blueprint. Take your time and cut one part at the time even if you have practiced making the same blueprint before. The test plate blueprint measurements could have been slightly changed without prior notice.
Use common sense and always follow correct safety procedures.
Inspect the entire work area and equipment paying close attention to electrical connections and any safety hazards.
Wear proper fitting work clothes that protect your entire body from molten metal, intense radiating heat, sparks, and electric shock. Never use baggy or loose clothes. You are working in a hazardous environment with moving machinery and power tools where you could easily be dismembered or burned. Don't wear pants, jackets, aprons or coveralls with exposed pockets, sleeves, or collars. You could be seriously injured if a 2000 degree molten metal object or spark gets caught inside your clothes. You will be tested on safety procedures and work space tidiness as well.
Clean and put all materials and equipment on their proper storage location before presenting your work for inspection.
Good Luck!
Comments
0 comment