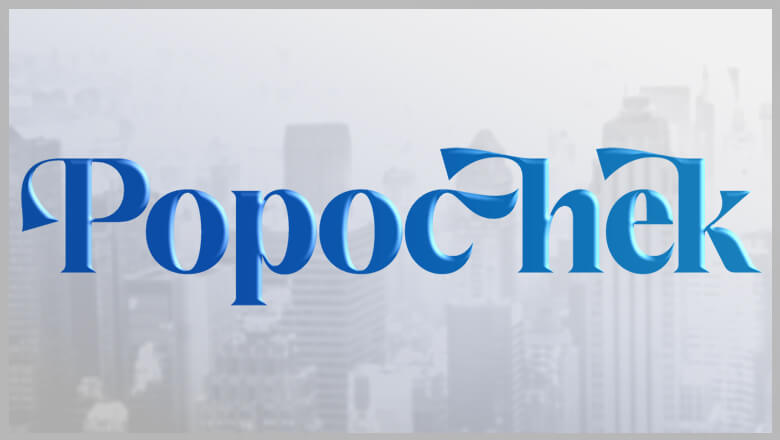
views
CHENNAI: How often we have run our fingers over the old, soft silk of our grandmother’s kanjeevarams, marvelling at the time and skill it must have taken to weave the sari and the delicate zari that adorns its ends! While the birth of the kanjeevaram has often been discussed, its disposal forms the very core of the sustenance of several goldsmiths whose livelihoods have revolved around removing and selling the zari (gold thread) from the sari for generations. It is common knowledge that zari-filled saris were considered a wise investment: not only did the sari last long, the gold thread could be exchanged for money. “When I was young, my mother exchanged all her old, torn saris for ever-silver vessels,” says R Seetha, a homemaker. “The man who came to our door to collect the sari would sell the zari to goldsmiths who’d melt it and give him a commission.” Several sari shops now take used saris and offer credit slips in return. The customer can choose a sari from the shop, and the shop benefits from the business. Others still prefer the conventional route of selling the zari to a goldsmith — artisans who, perhaps, have never received their due. The narrow, labyrinthine streets near Kapaleeshwar Temple in Mylapore are home to several such men of the craft.In an unassuming little house on CP Koil street, (Royapettah) is Suriya Centre, which has specialised in zari-melting for the last 40 years. The proprietor, Pramoth, a third generation smith, despite his reluctance, opened up when asked about the job he loves. “It’s a complicated process, a real craft,” he says, gesturing to the furnace, bath and silicon carbide crucibles of varying sizes that occupy the dark, cool room with its green walls and wooden windows. “The melting is done after we estimate the amount of metal used.” Pramoth says the costing also depends on the amount of silver used in the zari. “There are several different qualities of zari (with names like Napoleon, Meera and Meenakshi), and the quality indicates the amount of silver we can extract from it,” he says. Since different qualities are used for borders, intermediate designs and the pallu, the true value is calculated after the average cost of the metal used is determined.“Silver rates have gone up now; from `30 per gram a few years ago, it is now `74 a gram,” Pramoth says. Rising silver prices have increased the price of zari from `3,150 in 2005 to `11,500 per marc (equal to 242 grams) now. However, despite this and the fact that the process does not require more than a day and one person on the job, extracting the metal is an expensive proposition because the chemicals used have to be thrown away with every cycle. Also, the percentage of silver in zari has decreased rapidly, with weavers using other metals to cut costs. “The TN government has stipulated that one marc of zari should contain 55 to 57 per cent silver and 0.2 to 0.6 per cent gold, but private owners use artificial zari, which costs only about `300, to lower the costs,” says Pramoth. “Naturally, this affects our business as well.” Also, more people are buying saris containing tested (artificial) zari because they are cheaper.Pramoth believes the occupation faces the threat of extinction, just like many other hand-based skills that are withering away in the face of mechanisation. “Big dealers now possess large XRF analyser machines, which estimate the amount and value of silver used,” he says. “In a few years time, we will be redundant.” Though Pramoth wouldn’t want his children to have to earn their living in the manner he has earned his, he can’t help but rue the fact that the skill will soon be lost forever. “It’s a dying art,” he says. “Machines have taken over.”
Comments
0 comment